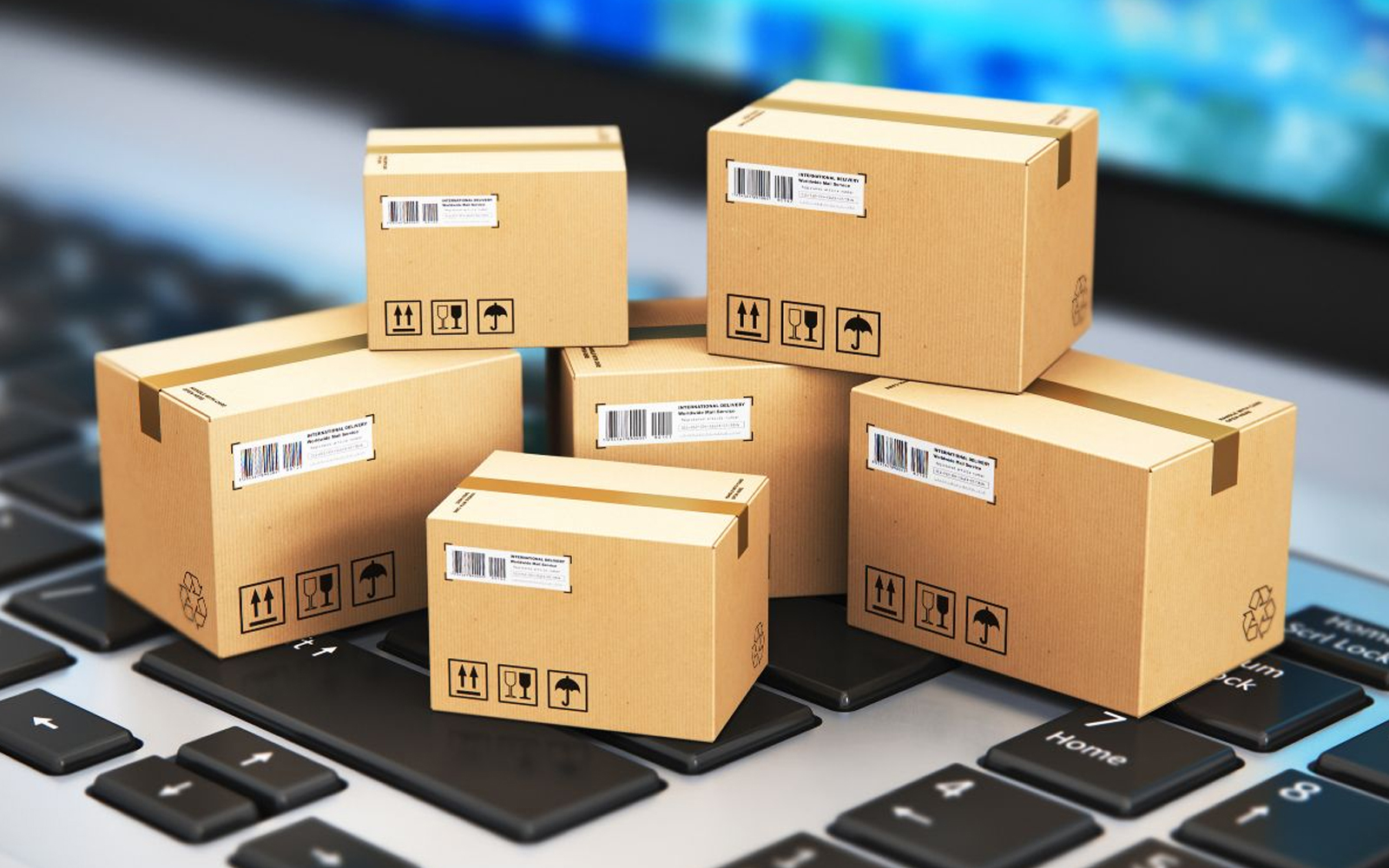
Any industry that manufactures goods works with the basic aim of delivering those goods to the end customers. Here’s where the industry’s supply chain comes into the picture.
The entire process from the storage of the manufactured goods (warehousing), packaging, transportation, and final delivery constitutes the supply chain. Every step in the process is extremely crucial & sensitive depending on the product. Needless to say, things become even more sensitive when dealing with pharmaceutical supply chain management.
Pharmaceutical Supply Chain Challenges
Out of the numerous challenges in the pharmaceutical supply chain, some of the most critical ones are:
- Warehousing
Each drug/medicine or vaccine needs specific conditions and temperatures to survive and maintain the desired composition. Hence, providing the necessary storage conditions for pharmaceutical products is of utmost importance.
- Regulations
The pharma supply chain has to comply with the necessary regulations, for instance, the Good Distribution Practices (GDP) accorded by the Societe Generale de Surveillance (SGS), the world’s leading testing, inspection, and certification company. Additionally, compliance checks and measures are required for the drug supply chain, even internally within the company.
- OTIF Delivery
On-time In-full (OTIF) delivery is a pharma supply chain standard. As per the standard, the delivery should also be In Full & On-Time – if any of the aspects is compromised (either the quantity or time delay), it is not considered a delivery at all. This requires robust packaging & logistics and real-time tracking of the product. The former would ensure no roadblocks during the journey. The latter ensures a timely damage control process.
- Rising competition & fluctuating prices
Markets are never 100% predictable – the unpredictability and instability increase in times of crisis, comprehensively exemplified by the recent pandemic. Likewise, the ever-increasing competition & fluctuating markets in the pharma industry add to pharma supply chain challenges. Quality & cost-effectiveness are the factors that ultimately attract the consumers.
- Current, cognizant, and resilient
It is very important to stay abreast of the markets’ latest, to implement the latest technologies to a) stay in the market, and b) reduce the processing time & costs to meet the demands & to build resilient pharmaceutical supply chain management. A single loose step can weigh more than a hundred successes!
All About VRL’s Pharmaceutical Supply Chain Management
Well, not all, but let’s peep into the drug supply chain funda of Venus Remedies Limited & all its subsidiaries and units.
FLOW OF SUPPLY CHAIN
- Receipt of Orders
- Received via a software
- The order is readied for dispatch if already available
- If not
- A product indent is created for the in-house manufacturing of goods, or
- The production is outsourced to a vendor
2. Warehousing
- The manufactured goods are received in the warehouse via temperature-controlled logistics
- Finished goods are initially placed in an untouched area allocated through 2D barcodes. Once approved by the Quality Analytics (QA) Team, these products are moved and allocated to the approved area.
- They are stacked in temperature-controlled areas as per the specification.
3. Documentation
a) Preparation of documents for order execution starting from pre-challan, invoice, packing list, gate pass, to the EWAY bill for transportation.
4. Transportation
- Identification of an appropriate temperature-controlled logistics provider for the shipment of the product.
- Shrink-wrapping or palletization of the products as relevant.
- Handing over to the transporter with complete documentation.
5. Tracking
- Online tracking of the consignment from dispatch to destination.
- Customer feedback upon receipt.
PROBLEMS FACED BY STAKEHOLDERS
During the entire supply-chain process, we become aware of various problems our stakeholders face. These problems, in turn, help us better our approach from time to time. Some of the issues that we realized & catered to include:
- A discrepancy between the actual product’s batch number and the one on the invoice
- Delay in delivery of products
- Delivery of the products in unfit conditions
SOLUTIONS
Implementing the barcode scanning system eliminated the problem of mismatch in the batch numbers.
We handpicked vendors that could fast-track the delivery process to avoid or at least minimize the delays. We made use of all modes of transport, i.e., roads, rails, and air, as per the feasibility. A minimum of 15 courier services and cargoes were impaneled for material dispatch. This change in strategy led to the achievement of more than 50% deliveries within 72 hours to the end customers.
For the intact delivery of the products, each package is shrink-wrapped to avoid any kind of damage due to unfavorable weather conditions, handling, etc. Additionally, the palletization system was incorporated to prevent the problem of breakage. We are among the first few companies that developed a palletization system in the pharmaceutical industry.
Other solutions that fast-tracked our operations include the implementation of the ERP software and an automatic tracking system (Raombee) for tracking the consignments. Performance of Data Loggers for temperature and humidity monitoring enabled us to achieve a temperature-controlled environment for our products.
CHALLENGES FACED BY SUPPLY CHAIN
Any organization or unit is bound to face challenges during its operations. The challenges range from management of human resources and lack of basic requirements to meeting the deadlines. The same was the case with our Supply Chain & Logistics Department. However, these challenges were crucial for the growth and betterment of our services & each person involved individually. Some of the difficulties inadvertently heightened during the COVID-19 pandemic. The circumstances, however, made us realize our potential and tap into resources that were otherwise unexplored. Some of the frequent challenges we faced and ways we devised to overcome them are:
- Manual tracing of the products/batches in the warehouse. It increased the risk of errors and involved extensive person-hours, also resulting in mixing or mismatch of batch numbers. We implemented the ERP software for the same.
- To ensure timely execution of orders during the manual process.
- Selection of the most appropriate courier/cargo service.
- Delayed reflection of payments in the system.
The logistical cost came as a major challenge during COVID-19; however, we did not increase a single penny in the freight cost. We were able to cater to these challenges through continuous efforts and fully automating the process. We’d want to come across more such challenges in the times to come so that our endeavor to improve and deliver better stays consistent.
Other challenges that we faced as a Corporate or from an Employees’ perspective:
- To ensure the safety of operations for our workers
For this, we incorporated automation tools like stackers, scissor lifts, hydraulic trolleys, shrink-wrapping machines, etc.
- To ensure error-free operations
For this, we implemented barcoding per the GS1 standards for location mapping and parent-child tracking in the packaging specification.
- To ensure economic & intellectual growth of employees
Regular training of employees for handling machines and ensuring error-free operations.
- To ensure capacity building with all our operations
We converted the entire workhouse into a production-like setup to increase the overall speed of the Order Execution process & facilitate automation.
- To ensure our production practices consistently refine towards creating a sustainable planet
We eliminated the use of plastic pallets and replaced the old motors and machines with new energy-efficient equipment.
- To ensure optimal logistics cost
Creating a seamless channel of logistical providers and ensuring transparency in the process.
- To ensure optimized packaging for all products
The entire start-to-end implementation of how our products are manufactured considering the logistics in mind. Whenever we create a new artwork in our product list, we ensure that the packaging design is optimized for shipping.
To overcome these challenges, we endeavor to have a technically driven supply chain industry. We have the same focus on supply chain & logistics. To summarise our accomplishments in the past that led us here –
1. Meeting challenges technologically
- Data logger/Raombee device for tracking of consignments
- 2D barcoding system for the products
- Development of a mobile application for seamless execution of orders & their delivery
- Implementation of SpineBMS software for inventory management and order execution
2. Resolving problems for the end customer
- Excellent packaging (shrink-wraps, temperature control measures, palletization, etc.)
- Using all modes of transport for quick & safe transportation of goods
3. Keeping the team motivated
- Safety measures at each step
- Installation of hydraulic trolleys and scissor lifts for ease of work
- Use of ERP software, 2D barcoding system, Data Loggers, Raombee, and mobile applications
4. Enhancing the performance at each level
- Automation, even at granular levels
- Training of employees to be abreast with the technological changes
- Renovation of the warehouse, considering the existing anomalies
- Measuring the outcome with the implementation of the aforementioned
5. Overcoming the challenging times
- COVID-19 & imposed difficulties.
- Meeting the customer requirements with a reduced workforce & other required resources.
- Taking care of the staff working during the pandemic. While the work was necessary, the staff’s health was never compromised.
6. Improving the journey & the end results
- Electrical stack for material loading in vehicles
- Selection of an apt cargo service & the vendors involved during the process
- Racking system for proper placement of products
- Taking time-to-time feedback to improve upon our methodology
- Actively ensuring customer delight – bank reconciliation through ROMBEA, Spine BMS & Davai App
- Strict adherence to timelines
All these efforts and much more led to our organization becoming debt-free last year. We’ve also been awarded for our Good Distribution Practices. Our team’s zeal and working spirit drive us to apply for this award, the winning of which will become an adding factor towards our better performance.
Latest Insights and Updates
Explore our latest articles on pharmaceuticals and healthcare.
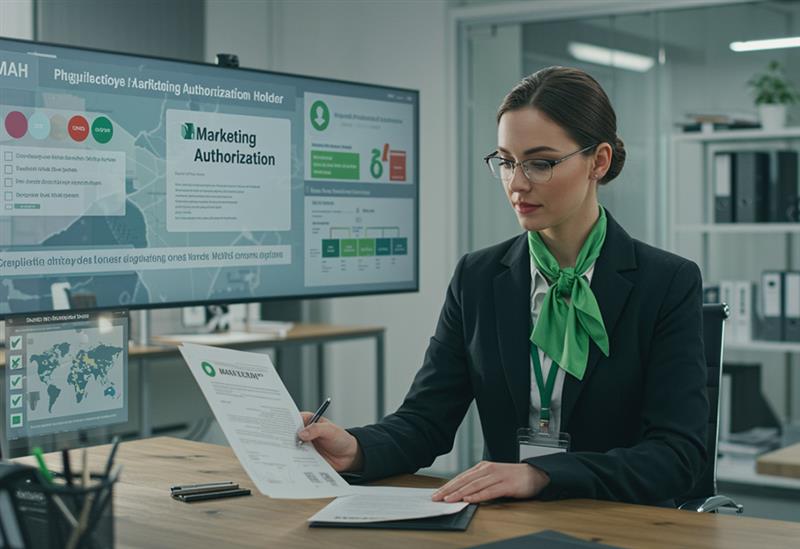